“Could it be a better result? By this, I mean should there really have been an extreme shortage and long lead times?” A fellow writer was an engineer at OnSemi. As he stated once, his job was watching the crystals (future “wafer material) grow. More coming on this comment shortly. You will not be experts (I am not either) in the process. Hopefully, you will understand why the issues associated with manufacturing semiconductors are questionable. I was purchasing for automotive and electronics companies following spec-sheets. I will offer an opinion at the end of this dialogue. The Silicon Wafer Production Process Silicon wafers result from the slicing of manufactured ingots which undergoes multiple processes before becoming a part of
Topics:
run75441 considers the following as important: Education, Featured Stories, Hot Topics, semiconductors, US/Global Economics
This could be interesting, too:
NewDealdemocrat writes JOLTS revisions from Yesterday’s Report
Joel Eissenberg writes No Invading Allies Act
Ken Melvin writes A Developed Taste
Joel Eissenberg writes How Tesla makes money
“Could it be a better result? By this, I mean should there really have been an extreme shortage and long lead times?”
A fellow writer was an engineer at OnSemi. As he stated once, his job was watching the crystals (future “wafer material) grow. More coming on this comment shortly. You will not be experts (I am not either) in the process. Hopefully, you will understand why the issues associated with manufacturing semiconductors are questionable. I was purchasing for automotive and electronics companies following spec-sheets.
I will offer an opinion at the end of this dialogue.
The Silicon Wafer Production Process
Silicon wafers result from the slicing of manufactured ingots which undergoes multiple processes before becoming a part of a semiconductor:
Ingot Growth
The first step in silicon wafer production is growing a nugget of silicon, also referred to as a silicon ingot. Growing a single silicon ingot can take as less as one week to up to one month. Size, quality, and the specifications of the wafer determines the time taken for the ingot growth. One of the most common methods used to grow the crystal is the Czochralski Method or the CZ Method. Processing using CZ process, consists of placing polycrystalline silicon pieces in a quartz trough.
Adding small quantities of dopants determines crystal properties. Dopants are elements from Group 3 and 4 of the periodic table. Boron, Phosphorus, Arsenic, or Antimony are Dopants. The properties of the resultant wafer material may be P (positive) type (Boron) or N (negative) type (Phosphorous, Arsenic, Antimony). Heating the material bove a temperature of 1412 degrees (usually above 1500 degrees) liquefies the crystal.
A silicon crystal having the same orientation (P or N) is the intended end result of the process is placed inside as a seed to facilitate the growth of the crystal with minimum defects. Once the diameter of the crystal, the process is stopped by stabilizing the conditions.
The resulting material is referred to as electronic grade silicon to EGS. Silicon ingots are cut and molded into the shapes needed for the final silicon wafers for the semiconductor.
Slicing
Ingot diameters are usually a little larger than what is in finishing specifications. The ingot goes through a slicing process creating the wafer after inspection. A diamond edge saw (or thin wire) process creates a thinner and smaller wafer without causing any major damage.
Lapping
Lapping is the next step in the process. It consists of removing the marks, abrasions, and defects from the sawing. This step also serves to thin out the wafer a bit more as well as relieve the stress that the wafer has undergone during the slicing process.
Cleaning
After lapping, the wafers pass through chemically etching and a cleaning process. This further helps to alleviate any cracks or surface defects that may still be there, even on a microscopic level. The bath consists of sodium hydroxide, acetic acid, or nitric acid.
Polishing
After cleaning, the wafer passes through polishing to reach its final stage. Performing wafer polishing is in a clean room where particle quantity per cubic foot of air is to Class 1 to Class 10,000 specifications. Workers have to wear clean suits, work under a fan that blows away excess particles, and maintain a level of cleanliness on their workstations. High quality silicon wafers usually go through two to three stages of polishing which can be a single side or double side polishing. Most wafers are subject to polishing on the front. The polishing process itself has two stages;
- The first stage being the stock removal process removing a thin layer of silicon to make sure the surface does not have any defects and
- A second stage of a chemical mechanical polish, not removing any silicon layers creating a shiny, mirror finish.
____________
What Happens after the Wafers are complete? “Packaging“
The silicon wafers go through polishing and pass through a series of cleaning baths. The wafers pass through inspections multiple times under high intensity lights to ensure there are no excess materials or defects on the surface. After the cleaning and inspection, the wafers meeting specifications go through packaging and sealed. Vacuum sealing the wafer in plastic packaging is important as to protect them from damage and keep moisture out. Upon the completion of packaging, the wafers go to Fabrication facilities and used as semiconductor substrates.
Better explained pictorially (click on it to make it larger)
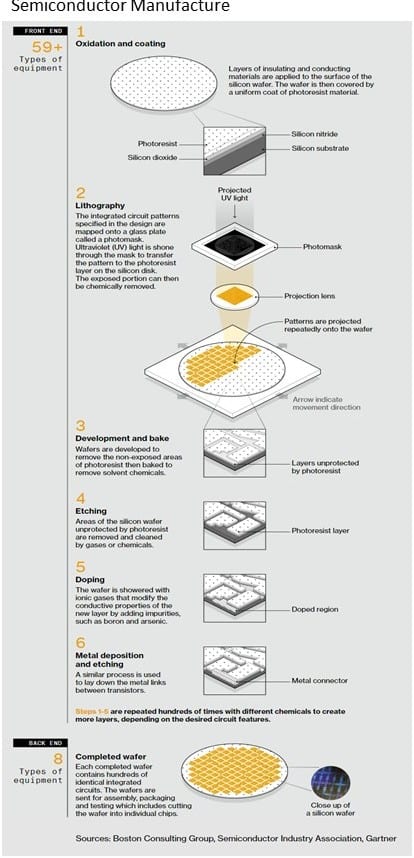
It was but a little more than a decade ago when the US was experiencing similar semiconductor shortages. My thinking back then was we will learn from the economic shutdown and prepare. Twenty twenty-one and we were no more prepared for an economic shutdown now as we were then. Closing down the economy shut down a low labor input manufacturing process which could have still manufactured semiconductors.
We are experiencing the same issues as what were experienced after 2008. We learned nothing from the last experience of maintaining orders and lead times. The planning of future orders stopped and orders canceled. No reserves were kept to cover a future startup. Today’s shortages did not have to be. There is a strong possibility the production process could have continued with little risk to people.